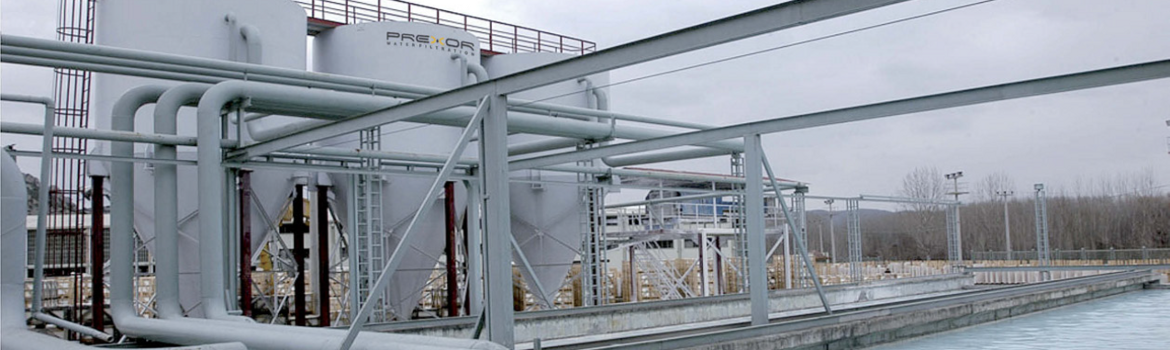
- Home
- Company
COMPANY
Prexor designs and realizes sewage treatment and filtration plants in many areas, among which the most important ones are:
ENGINEERING INSTALLATION
Prexor snc is specialized in supplying its worldwide customers with complete engineering services for sewage treatment and sludge treatment.
The Prexor design team collaborates with the customer by identifying the best system solutions, both in the case of complete supply of turnkey installations and in the case of expansion and modernization of existing plants.
Engineering focuses on all the main aspects of the plant: planes and views of the various manufacturing departments, machine foundation designs, service plan designs and drawings for power lines, water, compressed air and fuel.
Buying a Prexor plant or machine gives you access to a unique service package that meets your most specific needs.
A customer's order activates a process that develops throughout the product life: from design to after-sales service.
After evaluating customer needs, the Prexor team will elaborate an ad hoc plant proposal that takes into account space and machinery.
The design of each plant is provided using the most modern design systems: CAD - FEM - SOLID WORKS.
Feasibility studies: Identified the need of the customer, the Prexor business office presents the economic offer.
At the same time as the installation, Prexor provides the customer with specialized training personnel for the programming, correct use and maintenance of the machinery.
When designing and implementing its systems, Prexor follows the guidelines
ISO 9001: 2008 - Quality Certification. It contains a set of standards and guidelines developed by the International Organization for Standardization (ISO), which define the requirements for the implementation of a quality management system in order to conduct business processes, improve efficiency and efficiency in product realization and delivery of the service, obtaining and increasing customer satisfaction. The customer and its satisfaction are at the center of the ISO 9001: every activity, application, and activity / process monitoring is designed to determine the ultimate customer satisfaction.
ISO 14001 - Environmental Certification. Identifies an environmental management standard that the organization seeks by implementing an adequate management system to monitor the environmental impacts of its activities and systematically seek coherent, effective and, above all, sustainable improvement.
TECHNICAL ASSISTANCE - TRAINING – AFTER - SALES SERVICE
Prexor snc is able to provide efficient spare parts, assistance and services thanks to collaborative agreements specially designed for each single market in any continent. In this way, Prexor offers its customers quick, direct and effective service.
After sales service is developed in three ways:
Technical assistance service with immediate intervention guaranteed within short time by request via telephone or internet;
Technical assistance service by sending a qualified technician within 48h of the request, in case the problem can not be solved by phone or internet;
Provision of original, or compatible replacement parts if these were no longer in production.
A further key element of Prexor's success is the appropriate and continuous training of the personnel responsible for controlling production processes. Knowledge that is then transferred to the customer through training courses that can be carried out both at the company's headquarters and at customer establishments.
In addition, an e-learning project is being implemented, which will allow at any time a customized online and online trading directly at the customer's premises.
KNOW HOW
The Prexor Research Center is a valuable technological support for producers of sludge treatment and treatment plants.
One of the core services of the Research Center is the development of "tailor-made" solutions based on the characteristics of the granulometric and chemical analyzes.
The presence of a pilot plant provides adequate responses to the treatment of any kind of reflux.
To integrate this activity, the Research Center also offers customers the opportunity for technical and technological training, or to acquire the knowledge necessary for the future management of Prexor systems.
Continuous research and experimental activities are key strategic support for the development of new technologies (high efficiency pumping systems, compactness of the execution, reliability of the individual components of the plant, ...), and are realized with the possibility of sampling new products on a pilot scale.
The production of finished products, in collaboration with color printers and graphic studios, is a further service available to the customer.
- Stone industry
- Stone industry
- Ceramic industry
- Glass industry
- Steelworks
- Industrial laundries
Prexor snc is specialized in supplying its worldwide customers with complete engineering services for sewage treatment and sludge treatment.
The Prexor design team collaborates with the customer by identifying the best system solutions, both in the case of complete supply of turnkey installations and in the case of expansion and modernization of existing plants.
Engineering focuses on all the main aspects of the plant: planes and views of the various manufacturing departments, machine foundation designs, service plan designs and drawings for power lines, water, compressed air and fuel.
Buying a Prexor plant or machine gives you access to a unique service package that meets your most specific needs.
A customer's order activates a process that develops throughout the product life: from design to after-sales service.
After evaluating customer needs, the Prexor team will elaborate an ad hoc plant proposal that takes into account space and machinery.
The design of each plant is provided using the most modern design systems: CAD - FEM - SOLID WORKS.
Feasibility studies: Identified the need of the customer, the Prexor business office presents the economic offer.
At the same time as the installation, Prexor provides the customer with specialized training personnel for the programming, correct use and maintenance of the machinery.
When designing and implementing its systems, Prexor follows the guidelines
ISO 9001: 2008 - Quality Certification. It contains a set of standards and guidelines developed by the International Organization for Standardization (ISO), which define the requirements for the implementation of a quality management system in order to conduct business processes, improve efficiency and efficiency in product realization and delivery of the service, obtaining and increasing customer satisfaction. The customer and its satisfaction are at the center of the ISO 9001: every activity, application, and activity / process monitoring is designed to determine the ultimate customer satisfaction.
ISO 14001 - Environmental Certification. Identifies an environmental management standard that the organization seeks by implementing an adequate management system to monitor the environmental impacts of its activities and systematically seek coherent, effective and, above all, sustainable improvement.
TECHNICAL ASSISTANCE - TRAINING – AFTER - SALES SERVICE
Prexor snc is able to provide efficient spare parts, assistance and services thanks to collaborative agreements specially designed for each single market in any continent. In this way, Prexor offers its customers quick, direct and effective service.
After sales service is developed in three ways:
Technical assistance service with immediate intervention guaranteed within short time by request via telephone or internet;
Technical assistance service by sending a qualified technician within 48h of the request, in case the problem can not be solved by phone or internet;
Provision of original, or compatible replacement parts if these were no longer in production.
A further key element of Prexor's success is the appropriate and continuous training of the personnel responsible for controlling production processes. Knowledge that is then transferred to the customer through training courses that can be carried out both at the company's headquarters and at customer establishments.
In addition, an e-learning project is being implemented, which will allow at any time a customized online and online trading directly at the customer's premises.
KNOW HOW
The Prexor Research Center is a valuable technological support for producers of sludge treatment and treatment plants.
One of the core services of the Research Center is the development of "tailor-made" solutions based on the characteristics of the granulometric and chemical analyzes.
The presence of a pilot plant provides adequate responses to the treatment of any kind of reflux.
To integrate this activity, the Research Center also offers customers the opportunity for technical and technological training, or to acquire the knowledge necessary for the future management of Prexor systems.
Continuous research and experimental activities are key strategic support for the development of new technologies (high efficiency pumping systems, compactness of the execution, reliability of the individual components of the plant, ...), and are realized with the possibility of sampling new products on a pilot scale.
The production of finished products, in collaboration with color printers and graphic studios, is a further service available to the customer.
DOWNLOAD OUR
COMPANY PROFILE
COMPANY PROFILE